MTR is the leading supplier of membrane system for hydrocarbon recovery from petrochemical plant vents.
problem
Polyvinyl chloride (PVC) is produced by polymerization of vinyl chloride monomer (VCM). Unreacted VCM is pumped out of the reactor and condensed, and non-condensable gases are vented from the condenser. Depending on the temperature and pressure of the condenser, the vent stream also contains from 50 to 2,000 lb/h of VCM. As VCM emissions are tightly regulated, the vent stream must typically be incinerated and scrubbed before release.
VaporSep® Solution
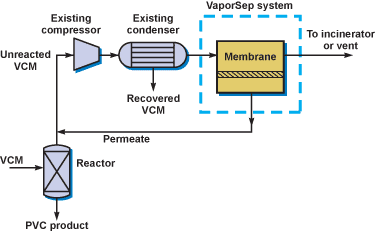
The vent stream from the existing VCM condenser is sent to the VaporSep system. VCM passes through the membrane at a greater rate than inert gases, producing a VCM-enriched permeate and a VCM-depleted residue. The permeate is recycled to the inlet of the existing compressor and the residue is incinerated. The VCM recovered by the VaporSep system is condensed in the existing condenser.
VaporSep systems allow PVC producers to recover 90% to 99+% of the VCM currently lost in vent streams, providing a significant economic benefit.
VaporSep systems are currently used by major PVC producers including Oxyvinyls, Westlake, Solvay, and Aiscondel.
Benefits
- Achieves significantly higher VCM recovery than possible by condensation alone
- Achieves recovery at more moderate temperatures and pressures than condensation alone
- Minimizes footprint and weight
- Minimizes maintenance with no moving parts
- VCM recovery up to 99+%
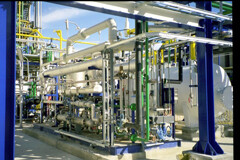
This VaporSep system recovers 1000 tons per year of VCM.
System Performance
- Complete, skid-mounted unit includes all necessary instrumentation and controls
- Unit dimensions: 6 to 15 ft (L) x 6 ft (W) x 6 ft (H); 5,000 to 15,000 lb
System Description
- Suitable for vent streams from 50 lb/h to greater than 2,000 lb/h, with VCM concentrations from 20 to 80 vol%